In modern industry, high temperature furnace is widely used in various industries, such as crystal growth, heat treatment, sintering etc.. Besides high melting point, low vapor pressures, low coefficient of thermal expansion, Tungsten, Molybdenum, Tantalum, Niobium and their alloys are excellent in high temperature strength and outstanding creep resistance, which can meet the strict requirements of materials for high-temperature furnaces. They are often used in the production of hot zones, heating elements and heat treatment vessels.
This type of high-temperature furnace is supporting operating temperatures between 900 ° C (1652 ° F) and 2800 ° C (5072 ° F). With rich experience in material R&D and furnaces structural design, Purex Metal provides reasonable design, selects suitable materials and produces high quality furnaces and related components depending on all your requirements.
Products:
1. Hot zones
2. Shieldings
3. Heating elements
4. Charge carriers
5. Crucibles
6. Sintering and annealing boat
7. Spare parts
8. Glass melting electrodes
1. Hot zones
According to each furnace design and the temperature and atmosphere inside furnaces, Tungsten, Molybdenum, Tantalum, Niobium and their alloys can be selected to make cylindrical, rectangular or special shaped heat zones chamber.
2. Shieldings
As the main component of the heat zones, shieldings can be riveted or welded into side shieldings and bottom shieldings, by using Tungsten, Molybdenum, Tantalum, or Niobium as materials.
3. Heating elements
The heating element is the heat source of the furnace. According to the different atmosphere and temperature requirements, it can use Tungsten heating elements, Tantalum heating elements or Rhenium heating elements. We can manufacture all kinds of heating elements depending on your drawings, we also provide thermal simulation and heating elements design in any size your needs.
4. Charge carriers
The shape of the heat zones is usually round or square. In order to make full use of the space inside heat zones, the charge carriers is essential. We provide the structure design of the charge carriers depending on the internal size of heat zones and the weight of product, which can fully meet the requirement of strength, reduce its own weight and save the cost.
5. Crucibles
Crucible is the most commonly used container for high-temperature furnace, generally used to hold solid-liquid raw materials, such as Al2O3 is used to grow sapphire crystal, and quartz sand is used to produce quartz glass, etc. We can provide integrated pressed crucible and formed crucible, we also provide welded crucible. The commonly used crucibles are Tungsten crucible, Molybdenum crucible and Tantalum crucible.
6. Sintering and annealing boat
The boat is also the most commonly used container for high-temperature furnace, generally used to hold solid raw materials, sintering or heat treatment. The commonly used boats are Tungsten boat, Molybdenum boat, Molybdenum Lanthanum boat, etc., which can be formed through mechanical processing, also be riveted and welded.
7. Spare parts
Screws, nuts, pins and rivets are commonly used as fasteners. In high temperature environment, fasteners are made of high melting point metals such as Tungsten, Molybdenum and Tantalum which are needed to fix the equipment and parts. We have standard fasteners for all your choices.
8. Glass melting electrodes
Molybdenum glass melting electrode has high melting point, high temperature strength and hardness, high thermal shocks resistance, good electrical conductivity and thermal conductivity, and corrosion resistance. It is easy to make pressure processing, mechanical processing, corrosion resistance to molten glass, corrosion products do not pollute glass, except lead removal glass, it is suitable for all kinds of glass manufacturing.
Molybdenum zirconium glass melting electrode: for the electrode deformation caused by gravity and glass wash under high temperature environment, we can provide a special electrode reinforcement scheme, which is adding a small amount of zirconia in molybdenum that can greatly enhance the sagging resistance and high-temperature creep resistance of the electrode.
Coated glass melting electrode: a special silicide coating on the surface of molybdenum glass melting electrode which can isolate the contact between the air and the electrode, thus to improve the service life of the electrode in oxidizing atmosphere.
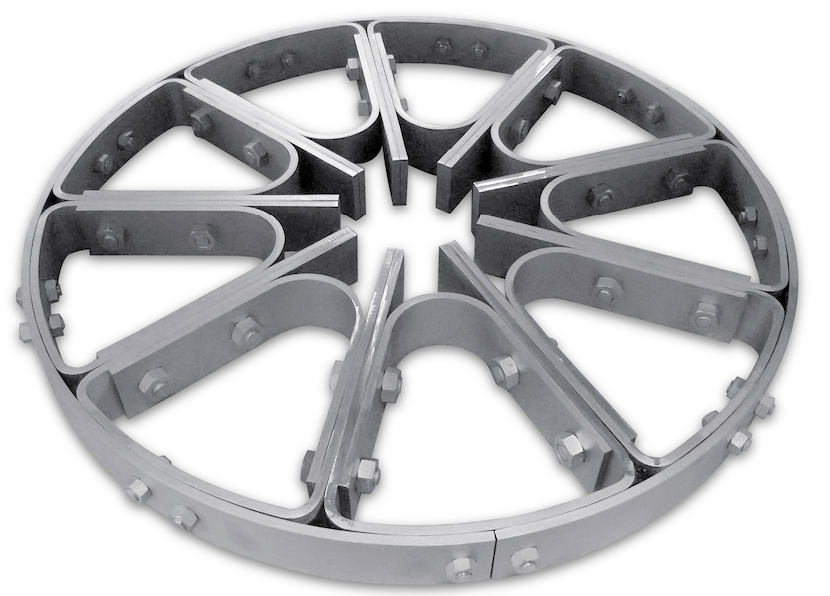
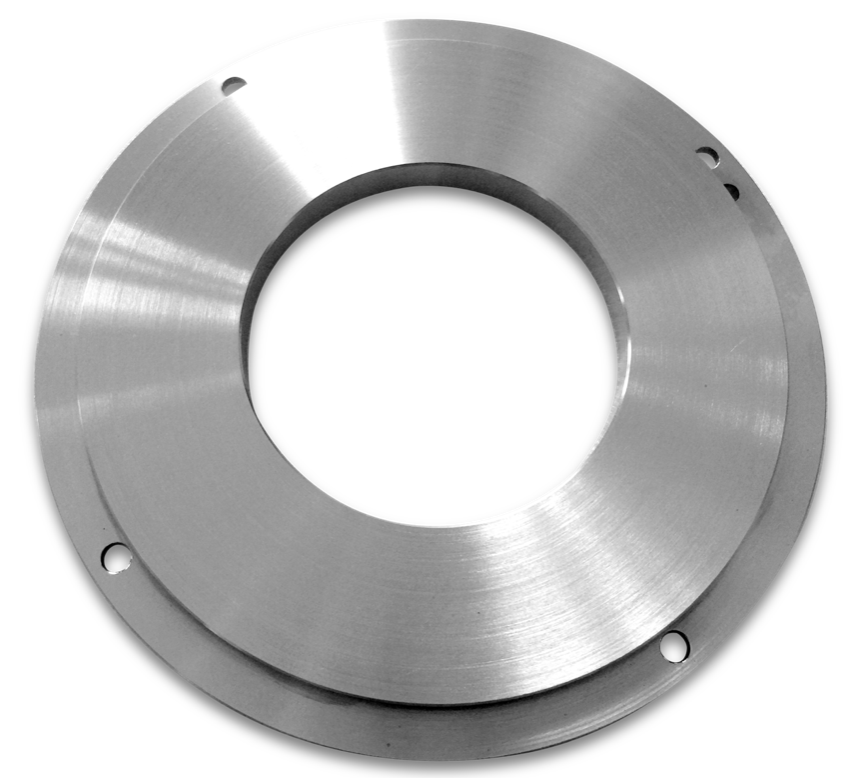